Quality, Health and Safety Manager
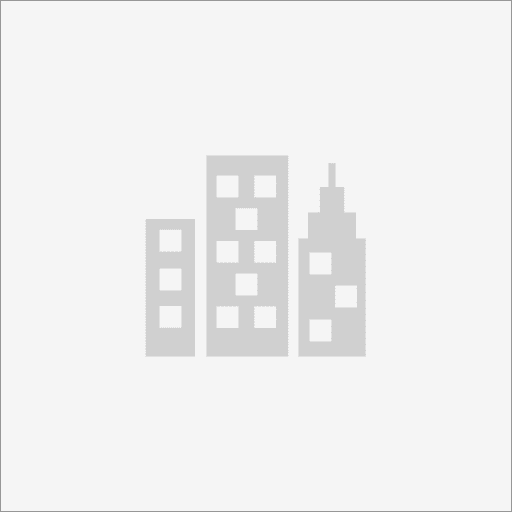
Hernshead Recruitment
Due to our continual growth, my client have a new position for a Quality, Health and Safety Manager.
- The Quality, Health and Safety Manager is responsible for ensuring the highest standards of Health and Safety and quality are maintained. They will be responsible for the Stores Team and all quality and Health and Safety matters.
- Their ideal candidate will have a mechanical engineering qualification or demonstrable experience. They will have an IOSH/NEBOSH qualification and sound knowledge of quality management systems.
- Candidates are required to have knowledge and experience of machine manufacturing/assembly with understanding of the requirements/expectations of current UK/EC & Global Machinery Directives. Knowledge or demonstrable experience of working with and conforming to the requirements and expectations of the Petrochemical Industries Standards would be advantageous.
The duties of the role are:
- To be the first point of contact for all H&S and Quality issues
- Ensuring the Company’s H&S/Quality policies and procedures are adhered to at all times
- Carrying out risk assessments and consider how risks could be reduced
- Carrying out regular site inspections to check H&S policies and procedures are being properly implemented and that the highest standards of quality are maintained at every stage of production.
- Investigating accidents and incidents and producing reports
- Keeping up to date with new legislation and maintaining a working knowledge of all Health and Safety Executive (HSE) legislation and any developments that affect the employer’s industry
- Lead in-house training with managers and employees regarding H&S and quality management
- Maintaining the company’s ISO 9001 accreditation and implement improvements where identifiable and appropriate.
- Reviewing and preparing quality documentation for release
- Undertaking dimensional checks as and when required within the manufacturing/assembly areas
- Working closely with the manufacturing, design and sales departments, on process validation, control, and procedural improvements
- Ensuring project level compliances are met and adhered to
- Investigating quality issues, understanding component interaction, driving to root cause and implementing corrective actions.
- Working with suppliers and internal departments to improve the overall end to end process.
- Managing the calibration of instruments used in manufacture, validation, & inspection.
- Developing protocols for inspection and evaluation of data
- Internal auditing/preparing reports to evaluate effectiveness of quality systems.
- Providing support for customers in terms of complaint handling, customer returns and ongoing quality support.
- Ensuring the inspection/measurement of ‘goods in’
- Carrying out first article, interim and final inspection of products as required.
- Undertaking dimensional checks as and when required within the manufacturing/assembly areas.
- Ensuring Quality/inspection paperwork completed as required.
- Ensuring that Quality/inspection procedures are followed.